RED.LINE – the premium extrusion line
Excellent profile quality. Lowest operating costs.
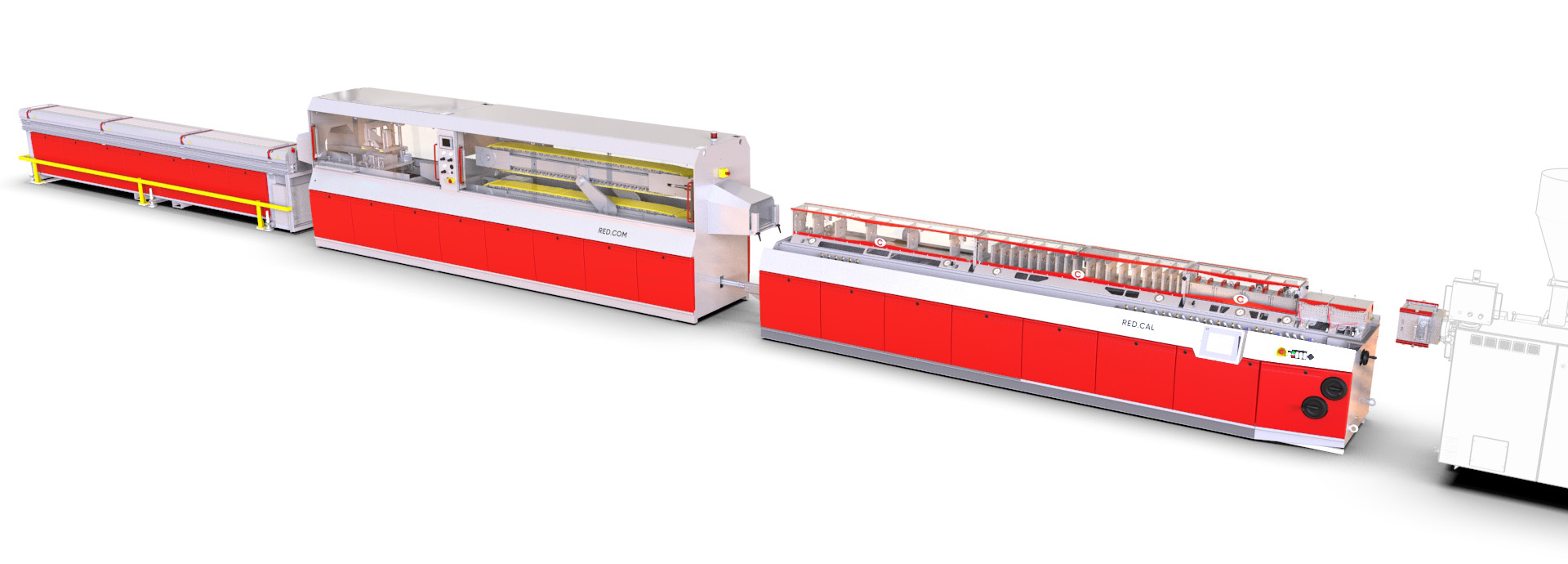
A weighing table to digitally monitor profile weight
Profile cutter and/or saw for cutting precision
Stable caterpillar or belt haul-off for safe profile withdrawal
An up to 28 m expandable calibration table with many extra features
as an intuitive, connected operating panel
Premium tooling for the most savings
The RED.LINE is a premium extrusion line with which you can achieve higher productivity, utmost process reliability and energy savings. It is perfectly tuned to the RED.TOOLING system.
RED.LINE uses a PLC control with a touch panel and has the tried-and-true Exelliq energy saving system GESS.TRONIC. The RED.CAL and RED.COM modules lead to the highest-possible savings in terms of energy and water consumption. What’s more, by using FLOW.CONTROL and FLOW.MATIC the functional dimensions can be assured within seconds and additional significant material savings can be guaranteed.
The RED.LINE machine systems are also designed as dual-strand constructions and are compatible with the Exelliq product portfolio.
- Utmost process reliability
- Maximum energy savings
- Maximum water savings
- Lowest production costs
- Improved handling
- Central production data logging
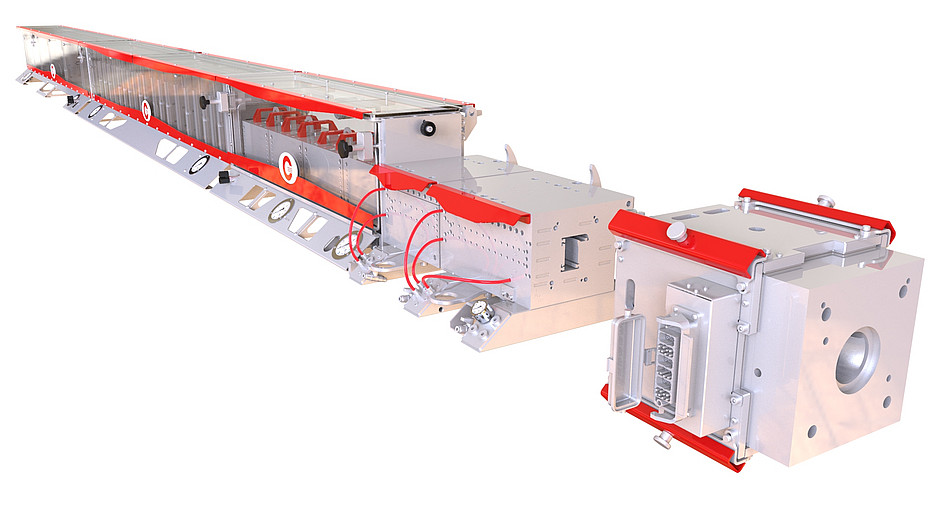
RED.TOOLING
Excellent profile quality. Lowest operating costs.
RED.TOOLING meets the highest requirements in plastic profile extrusion and is setting new standards with its unique features such as a heater cage with a central plug, PDC dry calibration, roller short calibration or options like FLOW.CONTROL and FLOW.MATIC, air support control,roller tuner, and the KEEP.CLEAN unit.
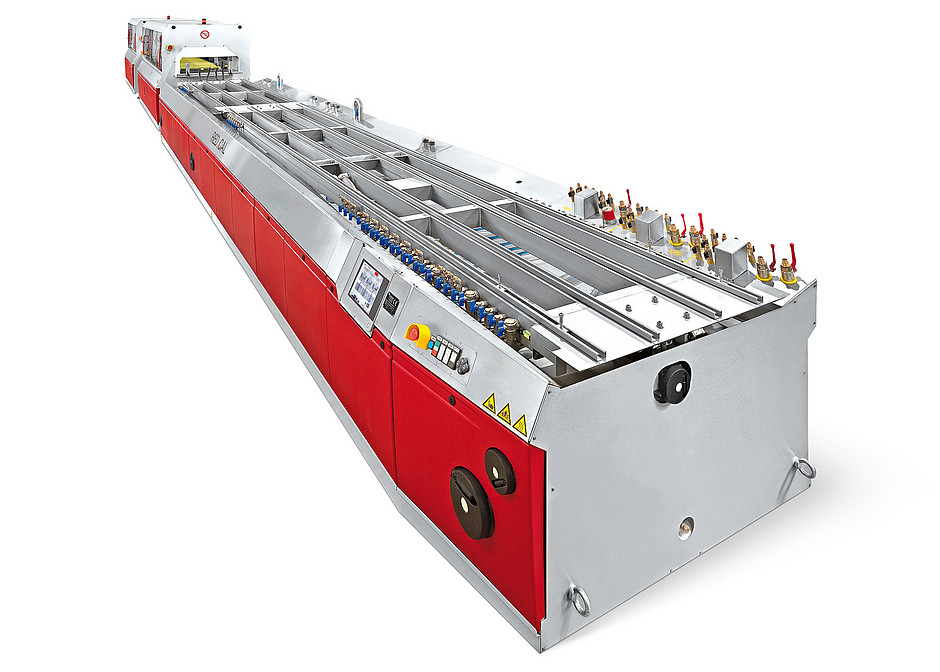
RED.CAL
The right choice for your extrusion.
Both the RED.LINE and RED.LINE basic machine systems come in a wide calibration table version (up to 1,000 mm). The increased process reliability arising from tried-and-true components and the flexibility from the equipment module system allow for not only single but also twin-strand construction, from a length of 4.2 m up to 28.0 m. Constant vacuum and ergonomic operating panels also offer easier, faster maintenance for improved handling.
GESS.TRONIC vacuum water energy management
Saves up to 90% in energy
- Reduces vacuum fluctuations to the technical minimum
- Avoids vacuum shocks, thus preventing profile surface defects
- Frequency-controlled cyclones provide a continuously stable vacuum and ensure consistently high profile quality
- Noise level cut in half
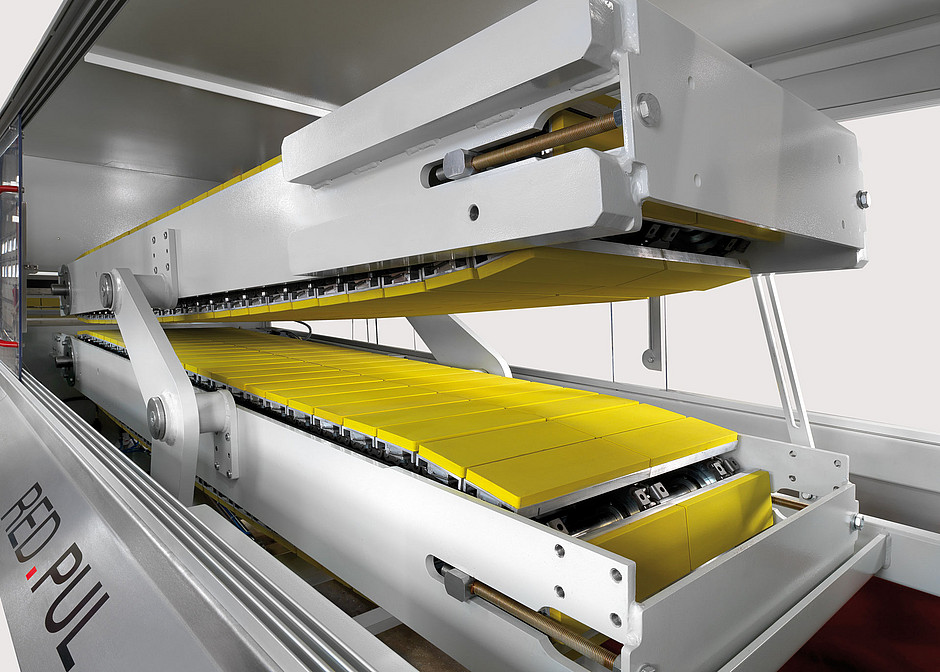
RED.PUL haul-off
Avoids tension on the profiles
- Prevents the pads from tipping over to leave imprints on the profile
- Quick replacement without requiring tools
- Cuts the set-up time in half
- Gentle profile withdrawal without it affecting the geometry of the profile
- Longer cleaning cycles for the pads because contact length is longer
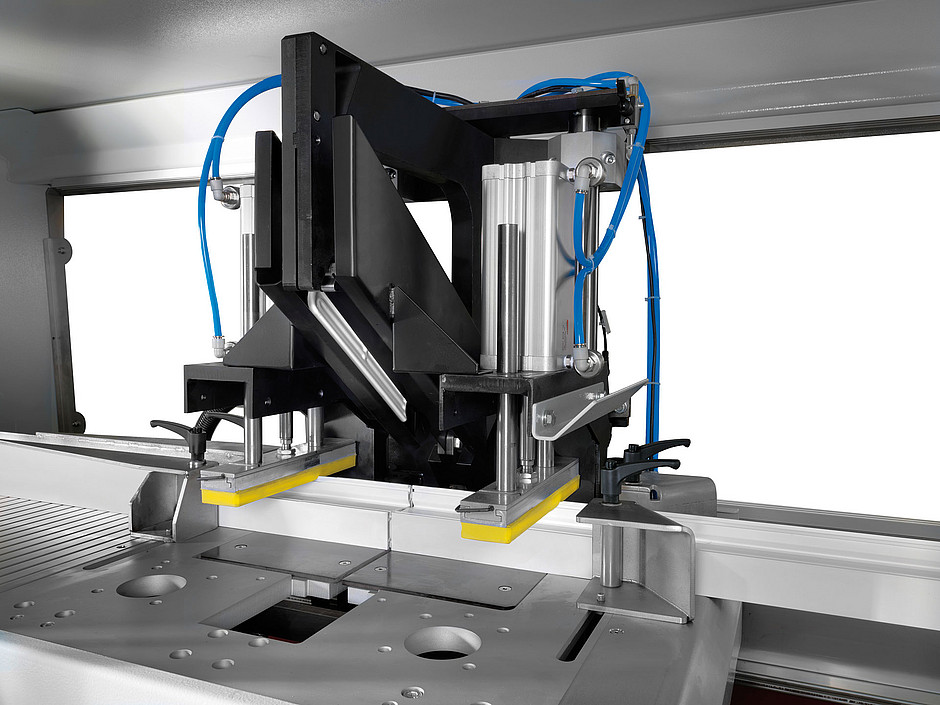
RED.CUT
Highest cut quality even with large profile cross-sections
- One blade for a profile width of up to 235 mm
- Variable cutting speeds for more flexibility
- Knife quickly replaced without requiring tools
- Savings through controlled knife-heating system for reproducible cut quality
- Clean separation
- NEW: RED.CUT C300 for profiles w 300 mm, h 200 mm
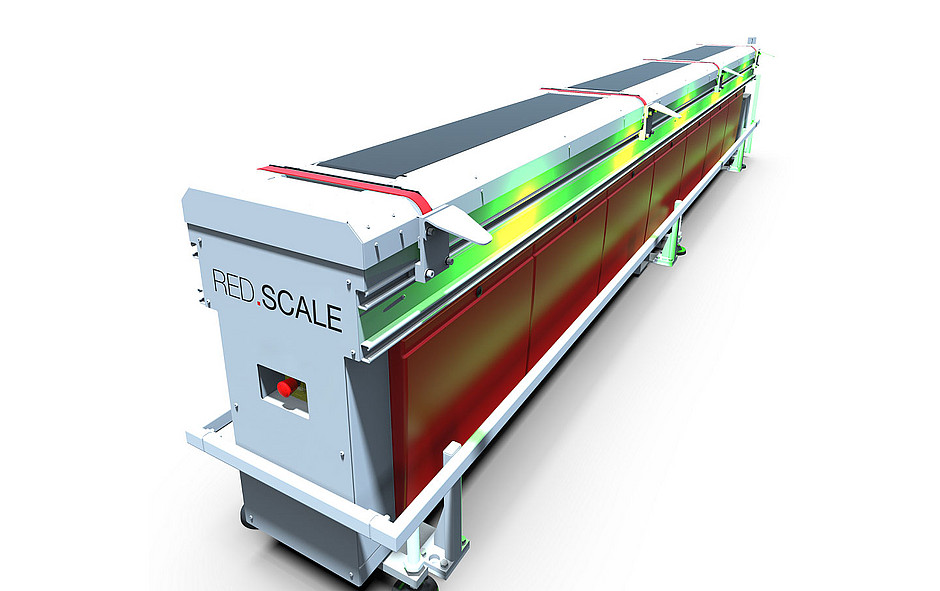
RED.SCALE
Digital profile weighing saves material costs
With the newly developed profile stacking end-component from Exelliq – the RED.SCALE with digitally integrated profile weighing – the amount of input material and the profile costs can be significantly reduced. The fast and precise weighing in combination with the permanent display of the current profile weight allows RED.SCALE to quickly and directly intervene in the event profile weights deviate during production. Thanks to seamless data recording, profile weight development trends can also be called up on the monitor at any time.
What’s more, Exelliq's RED.SCALE is equipped with an LED strip. It lights up green as long as the current profile weight is within the desired tolerance range. If the value is exceeded or falls below this range, the LED strip lights up in a different colour.
Your benefits:
- Precise in-line profile weighing
- Permanent real-time display of the actual profile weight
- Seamless data recording
- Display of trend lines in weight development on the RED.SCALE monitor and the RED.LINE control
- Quickly intervene in the process
- Significantly reduces the amount of input material
- Automatic stacking separated into approved products and rejects